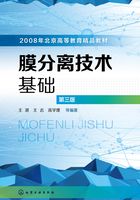
2.7 膜 缺 陷
2.7.1 膜的微观结构
可采用多种方法来揭示膜的微观精细的形态结构(层结构和孔结构)。一般可用千分尺、电子显微镜或透射显微镜精确测定膜的皮层厚度,而孔结构的测定方法较多。图2-13列出了用来表征多孔膜孔结构的主要表征技术[1]。

图2-13 多孔膜孔结构的主要表征技术
2.7.2 膜缺陷
膜分离是在分子级水平上进行的分离纯化。制备完美无缺的理想膜很关键。实际上,影响膜大规模工业使用更重要的因素是数量很少、按面积只占百分之零点几或更少的膜表皮或深层的孔穴。膜缺陷即孔穴的存在给膜的整体性能带来极为不良的影响,这将不能实现分子级水平上的有效分离和纯化并使膜的使用寿命降低。膜孔穴按照大小和形状分为三个层次、四种类型[28](表2-7)。
表2-7 膜孔穴的三个层次

四种类型分别为:①双眼皮型是穴口长型,穴边缘一侧较厚、光滑,另一侧较薄,中间围成一条沟,如人的双眼皮见图2-14(a);②鼠洞型为开口向上,穴口较圆,洞弯曲藏于膜表皮下,与纤维相连见图2-14(b);③筒状型为开口向上,穴口圆形,如圆筒由表皮直达纤维见图2-14(c);④云状型如小云团布于膜表面,构成一簇见图2-14(d)。

图2-14 膜孔穴类型
双眼皮型属于肉眼或灯光可见的第一或第二层次。其余三种属于第三层次。由于它肉眼或灯光下不可见,剪裁时不易避开,因而对膜性能有着更大影响。
实践证明,膜材料和配方不同时,在同一无纺布上制膜,其孔穴生成的大小、形状也有区别。如聚砜膜其孔穴一般为“筒状型”;聚砜酰胺其孔穴一般为“鼠洞型”。显然,这与高分子、溶剂、添加剂等和无纺布之间的作用力有关。
对于相转移法制得的膜而言,表面致密层仅有0.1~1μm,故缺陷在所难免。膜表层缺陷孔洞的生成有多种原因(气泡、尘埃、支撑纤维的缺陷等原因),比如对于一般的相转化制膜法(由刮膜或流涎、蒸发、冷浸、热处理等步骤组成)而言,其中蒸发步骤对非对称膜表层的形成及复合膜超薄层的形成尤其重要[29]。有学者认为:当铸膜液蒸发时,其气液界面不可避免地要受到某种随机扰动。若系统是稳定的,扰动会自动消除,气液界面仍保持平整;若系统是不稳定的,扰动将不断长大,在气液界面引起可观察到的凹凸不平或者孔洞类的结构。当铸膜液固化成膜时,上述结构也将固化在膜表面上,成为超薄致密层的表面缺陷。
对于膜厚大于10μm的非对称膜(铸膜液初始厚度约在50μm以上),Ray等认为溶剂的蒸发使气液界面形成很大的浓度梯度并产生界面处的过量分子作用势梯度,它是造成铸膜液气液界面对扰动不稳定的原因[30]。依据该机理对因不稳定而形成的膜表面结构特征进行的预测计算取得了满意的结果。而对于10μm以下厚度的超薄膜,特别是膜层很薄时,上面的Ray等的理论失效,因为此时膜层厚度与分子间作用力的有效范围处于同一数量级(0~100nm),此时支撑铸膜液的固体与铸膜液的分子间作用力将强烈地影响液膜的行为,出现缺陷孔洞的机会反而增多。当给液膜表面以小的扰动时,如果固液相间分子的作用力比液相自身分子的作用力大[即铸膜液能良好地湿润固体支撑物(例如无纺布)],这一扰动就将使系统的自由焓增加,根据热力学原理,扰动将可能自发消失;此时铸膜液越薄,越稳定。反之,固液相间分子的作用力小于液相自身分子的作用力[即铸膜液不能良好地湿润固体支撑物(例如无纺布)],那么扰动将使系统的自由焓减少,这种扰动就会不断长大,这时铸膜液系统就是不稳定的;铸膜液越薄,失稳的可能性反而增大。王志等根据实验结果确定的最佳膜厚范围为81~200nm。当超薄膜厚度处于这一范围内时,在具有高的透水率的同时还将具有高的截留率[29]。
对水溶液分离用的反渗透、超滤膜来说,这类缺陷影响相对较小。但对气体分离膜,气体以黏性流直接透过这些缺陷,将极大地降低分离性能。1976年Browall提出的解决办法是在膜表面再涂覆一层较易透过的材料,这层材料大大地减少了通过缺陷处的非扩散气流,而对无缺陷处的扩散气流则影响甚小[31]。基于此原理,Henis 以L-S法制成的聚砜膜,表面涂覆硅橡胶,成功地用于氢气分离[32]。