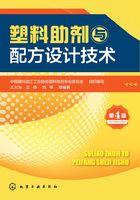
4.3 环境友好型高分子增塑剂增塑聚氯乙烯研究与应用进展
(徐国忠,柴瑞丹,张军)
PVC产品有硬制品和软制品之分,其中硬质PVC主要用于生产塑钢门窗、管材、板材等,软质PVC主要用于电线电缆、薄膜、人造革、制鞋等行业。在软质PVC的生产过程中,常常会加入增塑剂来降低PVC的玻璃化转变温度,使之在常温下具有橡胶的弹性。最初的增塑剂大多是小分子,如邻苯二甲酸酯类、脂肪族二元酸酯类和磷酸酯类等,它们的优点是可以大量加入且比例可调,柔韧性和弹性改性效果明显,缺点是部分邻苯二甲酸酯类增塑剂对环境和人体有害。小分子类增塑剂还存在易迁移、易抽出,制品容易失去弹性、开裂等不足。
2003年1月27日,欧盟议会和欧盟理事会通过了2002/95/EC指令,即“在电子电气设备中限制使用某些有害物质指令”(简称RoHS指令)。2006年7月1日以后,欧盟市场上已经正式禁止铅、镉、六价铬、汞等重金属以及多溴联苯、多溴联苯醚等六类有毒有害物质含量超标的产品进行销售。2006年12月18日欧盟议会和欧盟理事会还正式共同通过的《关于化学品注册、评估、许可和限制制度》法规(简称REACH法规),并也于2007年6月1日起生效,其中高度关注的物质种类高达近百种,包括邻苯二甲酸二(2-乙基己)酯、邻苯二甲酸二丁酯、邻苯二甲酸二异丁酯和邻苯二甲酸丁苄酯等邻苯二甲酸酯类增塑剂。
尽管小分子增塑剂具有增塑效率高、成本低的优点,但是易挥发、不耐抽出,而且邻苯二甲酸酯类增塑剂对人体和环境有害。高分子增塑剂,如聚酯类增塑剂、液体丁腈橡胶(LNBR)、粉末丁腈橡胶(PNBR)、杜邦公司推出的Elvaloy三元共聚物等,其成本较高且增塑效率低,但是近年来随着人们环保意识的提高以及为了提高制品的长期性能,高分子增塑剂再一次引起人们的注意。
本节简要介绍常用增塑剂的分类与特点,以及高分子增塑剂在PVC中的应用。
4.3.1 常用增塑剂的分类与特点
4.3.1.1 小分子增塑剂
邻苯二甲酸酯是最常用的增塑剂,占增塑剂总量的80%以上。如邻苯二甲酸(2-乙基己)酯(简称DOP,欧美国家又称DEHP)和邻苯二甲酸二丁酯(DBP)等,这类增塑剂与PVC的相容性好,增塑效率高,挥发性低,应用十分广泛。但是增塑剂易向PVC制品表面迁移,与食品接触时易被抽出;若PVC暴露在光照下会发生降解,加速了这一过程。
对苯二甲酸酯也是常用的一种增塑剂,主要是对苯二甲酸二辛酯(DOTP),它耐热、耐寒、难挥发、柔软性好、电绝缘性能好,常用于电缆料、人造革中,可部分替代邻苯类增塑剂。
脂肪族二元酸酯类增塑剂如己二酸二辛酯(DOA)、癸二酸二辛酯(DOS)等赋予了PVC制品良好的低温性能,主要用于薄膜、管材等,和对苯类增塑剂一起被称为耐寒增塑剂。
由于传统的邻苯二甲酸酯类增塑剂DOP、DBP等对人体、环境有潜在风险,目前在许多方面的应用受到了限制,人们又开发出新型环保增塑剂如柠檬酸酯增塑剂、环氧化合物等。
4.3.1.2 高分子增塑剂
高分子增塑剂即将大分子聚合物加入PVC中,起到增塑的效果,同时耐抽出性极佳。高分子增塑剂品种较多,有聚酯增塑剂、液体丁腈橡胶(LNBR)、粉末丁腈橡胶(PNBR)、乙烯-乙酸乙烯-一氧化碳三元共聚物(EVA-CO)和乙烯-丙烯酸正丁酯-一氧化碳三元共聚物(EnBA-CO)等。在一些对耐油性、耐溶剂性要求较高的场合,如与食品、医药接触时,可以用高分子增塑剂代替常用的小分子增塑剂,制作出易于印刷和包装的环保PVC薄膜制品。
高分子增塑剂在与DOP等小分子增塑剂共同使用时,特别要注意的是必须使PVC将小分子增塑剂完全吸收呈干粉状以后并降至常温时,再加入高分子增塑剂。否则由于高分子增塑剂与小分子增塑剂的相容性优于PVC和小分子增塑剂的相容性,使高分子增塑剂先吸收小分子增塑剂,导致PVC塑化不完全。
4.3.2 高分子增塑剂在PVC中的应用进展
4.3.2.1 PVC/聚酯增塑剂
聚酯增塑剂是应用较早的一种高分子增塑剂,主要由二元酸和二元醇通过缩合反应制得,种类有己二酸类聚酯和苯酐聚酯等,分子量在3000左右,它不仅耐抽出、不易迁移,并且能减少软质PVC中小分子增塑剂的迁移。聚酯增塑剂使PVC的加工性能提高,适用于耐油、耐水和耐溶剂的塑料制品如皮革、玩具、医药和食品等行业,在软质PVC中应用时添加量能达到70%。
相对分子质量和支化度影响聚酯增塑剂的增塑效果。随着聚酯增塑剂相对分子质量的提高,软质PVC的玻璃化转变温度下降,增塑效果和耐热性、耐溶剂性提高。聚酯增塑剂支化度的提高也提高了软质PVC的耐热性。
PVC/聚酯塑溶胶体系中,聚酯(如聚己二酸丙二醇酯,PPA)的适宜添加量为50~70(质量份),在此条件下塑溶胶的热稳定性能较好。目前汽车生产的涂装工序中大量采用“湿碰湿”技术,为了避免增塑剂被有机溶剂萃取,选择PVC/聚酯塑溶胶代替传统的小分子增塑剂体系,可取得良好效果。封端聚氨酯作为增塑剂添加时,也能使PVC/DOP/填料塑溶胶的剪切强度提高。
4.3.2.2 PVC/LNBR
液体丁腈橡胶是丁二烯和少量丙烯腈的共聚物,通过自由基乳液聚合方式合成,相对分子质量较小(相对分子质量一般在5000以下),常温下有流动性。最早为无官能团和无规官能团的品种,后来以端官能团类为主,如端羟基液体丁腈橡胶(HTBN)、端羧基液体丁腈橡胶(CTBN)、端巯基液体丁腈橡胶(MTBN)和端氨基液体丁腈橡胶(ATBN)等。这种含端官能团的橡胶在固化时,分子端部的官能团参与交联,使得硫化胶的交联网络中不含自由链端,交联点之间的相对分子质量比普通橡胶大,结构规整、无短链,因此柔软性很好。国产牌号主要是兰州石化的液体丁腈-26、液体丁腈-40和羧基液体丁腈等,结合丙烯腈质量分数分别为23%~27%、30%~34%、30%~35%。
将LNBR代替邻苯二甲酸类小分子增塑剂加入PVC糊树脂中,可制得耐溶剂、耐油性好的增塑聚氯乙烯材料,该材料不仅强度高、变形小,而且在正庚烷中的抽出率极低,可用于与食品接触的行业。
液体丁腈橡胶弥补了固体丁腈胶不易与PVC糊树脂混合的缺陷,因此可以用于改性PVC泡沫塑料。0~8(质量份)的LNBR使PVC泡沫塑料的拉伸强度、伸长率和硬度大幅提升,但是发泡倍率下降。LNBR在替代普通增塑剂如DOP、DBP等的同时,还可以改善PVC的弹性。将LNBR加入PVC/DINP(100/80)混合物中制成薄膜并测试力学性能,当LNBR的添加量为20份时断裂伸长率比未添加时增大一倍,同时拉伸强度没有下降。
4.3.2.3 PVC/PNBR
早在20世纪50年代,美国公司就开发出粉末丁腈橡胶,但技术不够完善,直到80年代才发展起来。粉末丁腈橡胶的优点主要体现在加工性能上。由于省去了切胶工序,可直接与配合剂混合进行加工,缩短混炼时间,减少加工时的热积累。
固特异(依里欧)公司生产的粉末丁腈橡胶P83(相对分子质量约20万),用PVC乳液包覆表面,主要用于PVC的改性,可以改善PVC的耐磨性、防滑性、耐低温曲挠性、压缩永久变形和恢复、耐溶剂抽出或温度升高时的增塑剂损失,熔体黏度的稳定性和耐油性等得到显著改善。
使用PNBR代替小分子增塑剂时,需要注意的是相同份数的PNBR的增塑效果不如DOP,但含PVC/PNBR混合物的拉伸强度和耐油性优于PVC/DOP。将PVC和增塑剂分别以70:30、60:40和50:50的比例混合制成热塑性弹性体,当增塑剂的含量从30份提高到50份时,弹性体的拉伸强度、硬度下降,其中含DOP的弹性体比含P83的弹性体下降更快。断裂伸长率随NBR和DOP的增加而升高,但DOP的作用更大。
在常温下应用时,P83在100份PVC、60~80份DOP、10~30份CaCO3和稳定剂等组成的软质PVC中,改变DOP、PNBR和CaCO3的含量,PNBR的添加使软质PVC在常温下、热老化后和耐油实验中硬度的下降减缓。
将增塑剂(柠檬酸酯/聚酯增塑剂)和NBR搅拌均匀后加入PVC糊树脂再搅拌均匀,再加入硫化剂进行化学交联制得环保型PVC/NBR浸塑手套,能减少材料的迁移和挥发。
将PNBR作为大分子增塑剂加入增塑PVC后混合物的耐老化性能提升。在增塑PVC的光老化过程中,小分子增塑剂DOP的在光照下发生降解和迁移,使增塑PVC的力学性能和弹性下降,而PNBR作为大分子增塑剂,不仅提升了增塑PVC的耐油性和耐抽出性,并且韧性也有所提高。同时在老化过程中,PVC/PNBR共混物的力学性能保持较好。但是由于PNBR结构中含有大量的1,4-反式丁二烯,在老化时易于引发共混物产生共轭双键,从而使制品颜色变黄。
4.3.2.4 PVC/乙烯三元共聚物
根据共聚单体的不同,乙烯三元共聚物可以分为乙烯-醋酸乙烯-一氧化碳(EVA-CO)、乙烯-丙烯酸正丁酯-一氧化碳(EnBA-CO)和乙烯-丙烯酸正丁酯-缩水甘油酯(EnBA-GMA)三大类。其中用作PVC增塑剂的主要是EVA-CO,杜邦公司的牌号为Elvaloy 741和Elvaloy 742等。我国在20世纪90年代也开发出国产EVA-CO,分为增塑型和增韧型两种,软质PVC改性用EVA-CO树脂中各组分为VA(20±2)%,CO(10±2)%。
EVA-CO三元共聚物的相对分子质量约为25万,与PVC的相容性好,同时,随着EVA-CO在共混物中质量分数的提高,共混体系的玻璃化转变温度也随之下降。当PVC/EVA-CO的质量比为70:30时,共混物的Tg为-6℃,当二者比例为50:50时,共混物的Tg下降为-29℃。大分子增塑剂的加入也起到防止小分子增塑剂迁移的作用。在PVC/DOP共混物中,当增塑剂DOP中的50w%被Elvaloy 742代替时,14天后测得增塑剂迁移率下降了2/3。EVA-CO的添加还能改善软质PVC在注塑和挤塑条件下的加工性能。
在力学性能方面,EVA-CO的添加使PVC/DOP体系的硬度、拉伸强度、撕裂强度和定伸应力有所下降,但伸长率提高。但是,在乳液共沉和熔体机械共混CR/PVC体系(共混比70/30)中使用时,2~4份的EVA-CO可以使共混物的拉伸强度和断裂伸长率有明显提高。EVA-CO也可以提高软质PVC的抗滑性能,当PVC作为鞋底材料使用时,15~30份的EVA-CO便可以达到防滑的目的。
由于EVA-CO具有良好的耐磨性、耐迁移性,从而广泛应用于制鞋、防水卷材、汽车内饰、电线电缆、医用制品和胶管等行业。
4.3.3 结论
高分子增塑剂虽然增塑效果不如小分子增塑剂,但是对软质PVC的强度、耐油性、耐溶剂性和耐热性等性能的提高优于小分子增塑剂。因此,随着各国环保意识的提高和一系列法规的颁布实施,对PVC制品中有毒有害增塑剂的限制,使得高分子增塑剂的发展壮大势在必行。