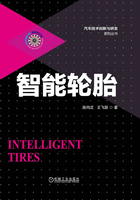
2.2 轮胎温度特性分析
轮胎温度是轮胎的一种非常重要的状态,随着轮胎的高速旋转,轮胎温度会发生一定程度的变化,轮胎温度的变化影响轮胎的安全性。轮胎温度变化受到外界环境温度、车速、轮胎载荷、轮胎压力等多种因素的影响,通过对这些因素的调节可以改变轮胎温度变化的过程,改善轮胎的运行安全性,另外,结合轮胎温度变化相关的影响因素进行轮胎温度变化过程的分析,可以更加准确地判断轮胎的故障情况,因此对轮胎温度特性和影响因素的分析是智能轮胎进行轮胎状态监控和故障诊断的基础。
下面首先分析轮胎温度变化对轮胎性能的影响,阐述保持轮胎温度安全对轮胎性能的重要性,然后从理论上对轮胎温度变化的过程进行分析,建立轮胎温度变化的理论模型,并通过实验对轮胎的温度变化过程进行测试验证,最后,分析轮胎温度变化影响因素的测试结果,总结各种因素与轮胎温度变化之间的关系,从而为智能轮胎进行异常状态故障的分析和诊断奠定基础。
2.2.1 轮胎温度变化对轮胎性能的影响
轮胎温度变化是轮胎滚动过程中产生热量的外在表现形式,轮胎滚动过程产生的热量越多,轮胎温度就上升得越快。随着轮胎温度的升高,轮胎的强度、弹性以及使用寿命等性能都逐渐下降。轮胎的温度升高将改变轮胎的力学物理性能和化学性能,甚至引起轮胎爆破和汽车燃油消耗的增加[1]。下面进行具体的分析。
(1)轮胎温度升高改变轮胎的力学物理性能,缩短轮胎的使用寿命
轮胎温度升高加速了轮胎橡胶的老化,使轮胎胎体材料的拉伸强度和耐磨性能等物理性能下降。轮胎在使用过程中的慢性损伤,如:肩空、肩裂、胎面磨损等一般都是由于高温下材料强度降低,在热疲劳作用下引起表层橡胶分子机械断裂而造成的[1]。
如图2.1所示,当轮胎温度从0℃升高到100℃时,对于普通轮胎来说,帘线的强度将降低12.5%,橡胶的强度将降低17.5%,特别是当轮胎温度高于其临界温度(100~121℃)时,轮胎的生热会急剧增加,橡胶和帘线强度将明显下降,当轮胎温度超过硫化点(140℃)时,轮胎的各组成部分将被破坏,失去承载能力,此时轮胎会由于强度不足而发生爆胎,所以轮胎的温度变化对其安全性和使用寿命的影响极大。统计显示,轮胎温度变化与轮胎的行驶里程之间存在图2.2所示的关系,当轮胎温度升高时,轮胎的行驶里程下降很快。

图2.1 拉伸强度与温度的关系图[2]

图2.2 轮胎温度变化与行驶里程之间的关系
(2)轮胎温度升高将导致轮胎内部的化学效应,加速轮胎橡胶的氧化和热降解过程
随着轮胎温度的升高,轮胎内部的橡胶会发生不同的化学效应,伴随着软化过程,天然胶可能引起断链,伴随着硬化过程,丁苯胶等可能形成附加的交联键。另外,轮胎温度升高加速了轮胎橡胶的氧化和热降解过程,过高的温度导致轮胎胎腔内气体更容易透过轮胎部件,从而使橡胶接触更多的氧气而加速氧化和热降解过程,引起轮胎内压力损失,轮胎产生较大的下沉量,受热状况进一步恶化。特别是,当轮胎橡胶热降解过程生成的气体聚集到一定程度后,会引起轮胎的爆破,造成严重的交通事故。
(3)轮胎温度升高增加了轮胎的接地面积,导致轮胎滚动阻力增大和汽车燃油消耗增多
随着轮胎温度的升高,轮胎接地面积增加,导致轮胎的滚动阻力增大,汽车的燃油消耗增多。滚动阻力是汽车行驶过程的主要能量损失,根据文献[3]仿真结果,轮胎温度影响轮胎的接地面积,轮胎温度升高,轮胎接地面积增大,因此,轮胎在路面的滚动阻力增大,汽车的耗油量增加。
2.2.2 轮胎温度特性理论分析
轮胎的温度升高主要由滞后生热和摩擦生热两种原因引起[1][4]。滞后生热是轮胎在地面接触发生变形过程产生的,轮胎在滚动过程中,轮胎的胎肩和胎侧橡胶发生弯曲变形,轮胎与路面接触区域发生径向压缩变形,由于橡胶的黏弹特性,使得轮胎在与路面反复接触与分离的过程中产生往复式的形变,由于应力与应变的不同步,压缩形变阶段储存的能量,在放松阶段部分释放出来,其余能量则转变成热能,造成了轮胎温度的升高。当外界条件改变时,例如载荷和速度增大、充气压力降低、道路起伏和多弯等,则轮胎的应变加剧,轮胎的滞后生热率增加,轮胎温升速度加快。摩擦生热是轮胎与路面发生摩擦引起的,特别是当汽车在加速、制动及急转弯的情况下,轮胎与路面的摩擦比较大,摩擦产生的热量部分流入地面,部分通过轮胎胎面进入胎体,引起轮胎温度升高。
在轮胎正常滚动过程中,滞后产生的热量是轮胎温度升高的主要原因,为了简化分析,下面采用滞后生热理论,通过轮胎滚动过程的能量转换关系建立轮胎温度变化的理论模型,对轮胎温度升高的过程进行研究,从而分析影响轮胎温度变化的内在因素。
当汽车轮胎在高速滚动行驶时,轮胎的橡胶材料发生周期性的应变,假设瞬时应变为[1]:

式中,ε0为最大应变;t为时间;ω为应变变化的圆周频率。
应变比应力变化慢,存在滞后,假设瞬时应力为[1]:

式中,,为储存弹性模量;
,为损耗弹性模量。此时,在每个旋转周期内轮胎橡胶滞后变形所做的功可用下式求解:


轮胎每个周期的应变做功所消耗的能量转变为热能使轮胎温度升高,根据能量守恒定律,利用式(2.3),轮胎在接地旋转时,每旋转一周所产生的热量为:

式中,tanδ为轮胎能量损耗因子,其数值越大,能量损耗越大,轮胎的生热量越大,它与轮胎所用材料的性能有关。
根据式(2.4)可以建立轮胎温度变化的理论模型为:

式中,ΔT为轮胎温度变化;L为轮胎厚度;k为轮胎材料导热系数;A为轮胎的散热面积。由式(2.5)可以看出,影响轮胎温度变化的内在因素是轮胎的性能参数、结构参数、转速ω和时间t,轮胎的性能参数包括储存弹性模量E′、最大应变ε0、轮胎能量损耗因子tanδ和轮胎材料导热系数k,轮胎的结构参数包括轮胎厚度L和轮胎的散热面积A。轮胎的温度变化与轮胎的转速ω、轮胎厚度L、最大应变量的平方、轮胎能量损耗因子tanδ和轮胎储存弹性模量E′成正比,与轮胎材料导热系数k、轮胎的散热面积A和轮胎运动时间t成反比。
2.2.3 轮胎温度特性实验研究
轮胎的温度变化过程受到多种因素的影响,式(2.5)描述的轮胎温度变化理论模型是在理想情况下,单位体积内的轮胎温度变化过程,实际的轮胎结构非常复杂,胎冠、胎侧、胎体以及胎内各部分的情况都不一样,利用式(2.5)难以描述具体的温度变化过程。常用的研究方法是通过有限元方法求解轮胎各部位的情况[5]-[14],但是最直接的研究方法还是实验研究,通过实验可以真实地反映轮胎表面的温度变化过程,并可以观察轮胎转速、充气压力和载荷等因素对轮胎温度变化的影响。
实验研究的轮胎温度变化过程主要包括汽车起动、加速和制动三个过程。当汽车起动后,轮胎开始滚动,此时轮胎温度和周围环境的温度相同,轮胎处于热平衡状态;汽车加速后,轮胎继续滚动,由于轮胎橡胶和骨架材料的滞后损失以及轮胎与路面之间的摩擦生热,轮胎温度逐渐升高,进入非稳态阶段,但是轮胎的温度不是持续上升的,当轮胎的生热速度与散热速度达到动态平衡时,轮胎的温度也达到了新的平衡状态,此时温度变化进入饱和区,基本不再变化;汽车制动后,轮胎逐渐停转,此时轮胎不再生热,进入散热阶段,轮胎在滚动过程中产生的热量向轮胎内部空气、轮胎周围空气散发,还可以通过轮辋向周围环境散发,轮胎的温度开始下降。
文献[15]~[18]利用高速轮胎转鼓试验台模拟轮胎的加速和制动过程,利用红外辐射温度测量方法进行轮胎表面温度变化过程的实验测试研究。红外辐射温度测量方法是一种进行高速滚动轮胎温度测量的理想方法,它可以不破坏测量温度场,实现非接触和远距离测量,反应速度快,灵敏度高。
实验轮胎为载重斜交轮胎(9.00 -20 PR12),轮胎转速为70km/h,施加载荷为18kN,轮胎内部初始压力为480kPa。轮胎表面不同部位(胎肩、胎侧和胎冠)的温度变化过程如图2.3所示,由图可以看出,初始的15min,轮胎温度上升较快,大约45min之后,温度上升十分缓慢,轮胎温度进入饱和区,此后一直到90min为止,轮胎表面温度几乎没有变化,此时生热与散热几乎平衡。轮胎各部位温升趋势基本一致,只是温升大小不同,其中胎肩部位温升最高,胎侧次之,胎冠最低。根据式(2.5),胎肩部位的胎体厚,生热量多,热量积聚的多,因此表面温度最高;胎侧部位胎体薄,散热快,因此温度不是很高;而胎冠部位刚性较大,变形较小,生热少,因此温升最低。

图2.3 普通斜交轮胎9.00-20 PR12在70km/h、480kPa和18kN载荷下表面不同位置的温升曲线[15]
在不同速度下轮胎胎冠部位的温升曲线如图2.4所示,由图可以看出,在不同速度下,温升时间一致,温升大小却不一样,速度越高,温升越大。根据式(2.5),随着速度的提高,轮胎变形频率加大,单位时间内生热量增多,因此温升增大。进一步研究表明,定载、定压及不同速度下,轮胎表面其他部位的温升情况与上述结论相似,且温升时间与轮胎旋转速度无关,因此不能用提高旋转速度的办法来尽快达到热平衡状态。另外,对不同载荷作用下的轮胎温度变化情况进行研究,结果显示,载荷越大,轮胎表面的温度上升得越快,但是温升时间和达到热平衡的时间不随载荷的变化而变化,因此,轮胎表面温度的上升趋势和达到稳态温度的时间几乎不随轮胎旋转速度和载荷的变化而变化。

图2.4 普通斜交轮胎9.00-20 PR12在480kPa初始压力、18kN载荷和不同速度下胎冠部位的温升[15]
通过上面的分析可以看出,轮胎在各种工况下的温升时间历程趋势具有一致性,温升曲线呈指数形式,使用条件只影响温升的大小,并不影响温升时间。在轮胎温升阶段,无论是轮胎内部各部位还是轮胎外部各部位,轮胎温升时间相同,影响轮胎温升的因素(速度、载荷、胎压和环境温度)对轮胎温升时间都没有影响,只影响轮胎各部位的温升大小,文献[18]应用最小二乘法,拟合得到描述轮胎温升时间历程变化的关系如下:

式中,ΔT为温升,单位为℃;t为时间,单位为min;T∞为轮胎稳态温度,单位为℃;T0为轮胎初始温度,单位为℃;ξ为轮胎温升快慢程度系数,其取值与轮胎部位及环境等因素有关。
在不同速度下测试轮胎胎肩部位的表面温度自然下降曲线如图2.5所示,由图可以看出,曲线呈指数形式随时间逐渐下降,这是由于轮胎内部材料的传热系数和轮胎表面与空气的对流换热系数及热辐射系数不同所致。轮胎内部温度高于轮胎外表面温度,热量由内部通过轮胎材料传到轮胎外表面;轮胎外表面的温度高于外部环境温度,轮胎外表面热量通过对流和辐射散发到周围环境中,直到与周围环境达到热平衡。轮胎内表面与胎内气体接触进行热扩散,由于从内表面的热扩散比外表面要小得多,因此,可以忽略不计。由图可以看出,轮胎自然冷却至室温的时间大约为3h,前60min轮胎温度下降较快,以后越来越慢,直至180min才达到室温。虽然速度不同时,轮胎表面温度不同,但是温度下降至室温的时间相同,说明轮胎表面的散热特性与速度无关。进一步研究表明,轮胎表面各部位温度冷却至室温的时间与速度、载荷及充气压力等因素都无关,因此轮胎表面温度的下降趋势和达到外界环境温度的时间几乎不随轮胎旋转速度、载荷和充气压力的变化而变化。

图2.5 普通斜交轮胎9.00-20 PR12在480kPa初始压力、18kN载荷和不同速度下胎肩部位的温度下降[15]
文献[18]应用最小二乘法,拟合得到轮胎表面温度下降随时间变化的函数关系式如下:

式中,a0、a1、a2为与轮胎表面部位、速度、载荷和充气压力等因素有关的系数。
通过对轮胎温度变化过程实验测试结果的分析可以看出,轮胎的载荷和速度对轮胎表面的温度变化影响较大,随着载荷的增加,轮胎变形增加,生热量增加,轮胎温度升高,随着轮胎旋转速度的增加,轮胎单位时间内的变形次数增加,生热量增加,轮胎温度也升高。但是,轮胎表面的温度变化在不同速度和不同载荷条件下具有相同的变化规律,轮胎表面温度从室温上升到稳态温度的时间基本相同,增长规律一致,呈指数变化曲线,停机后,轮胎温度下降到室温的时间基本相同,下降的规律也是一致的,呈指数分布形式。
2.2.4 轮胎温度影响因素分析
轮胎的温度变化不但与自身的材料和结构等内在因素有关,还与轮胎的转速、载荷、充气压力以及环境温度等外在因素有关。根据轮胎的材料和结构等内在因素对轮胎温度的影响,可以进行轮胎的优化设计来改变轮胎的温度特性。根据外在因素对轮胎温度的影响,可以改变外在因素来调节轮胎的温度特性,提高轮胎的安全性和经济性。下面主要研究轮胎外在因素对轮胎温度特性的影响,为轮胎的温度异常检测和智能调节提供理论基础。
文献[19]利用有限元仿真的方法研究了速度和压力对轮胎温度变化的影响,文献[20]利用有限元仿真了不同压力、气温、载荷和速度条件下的轮胎温度变化,显示了轮胎充气压力、气温、载荷和速度对轮胎温度变化的不同影响。文献[21]通过实验测试和有限元分析,验证了载荷和充气压力对轮胎温度变化的影响,随着载荷的增加,轮胎的温度呈上升趋势,随着充气压力的增加,轮胎温度呈下降趋势。文献[22]利用生热理论建立了轮胎表面的温升理论模型,解释了轮胎转速、载荷和压力对轮胎温度变化的影响,随着转速的增加,轮胎的变形频率增加,轮胎温升增加;随着轮胎压力的增加,轮胎刚度增大,轮胎变形量变小,轮胎温升下降;随着轮胎载荷的增加,轮胎变形量变大,轮胎温升增加。文献[23]通过有限元方法分析了轮胎形状、充气压力、载荷、速度、路面状况和环境温度对轮胎温度变化的影响,发现载荷对轮胎温度变化的影响较大。
为了深入研究不同外在因素对轮胎温度变化的影响,文献[24]通过实验测试获取了不同速度、载荷、压力以及环境温度条件下的温升测试数据,然后利用回归分析的方法建立了轮胎的温升与各种外在因素之间的关系。实验轮胎的规格为国产9.00-2014 PR尼龙斜交胎,普通纵向花纹(花纹条数为5),轮胎外直径为1018mm,轮胎断面宽为259mm,胎冠厚为31.5mm,胎肩厚为1.25mm,轮辋规格为7.0 T,轮胎标准载荷为25.235kN,轮胎标准压力为770kPa。
稳态时,实验测试得到轮胎胎肩表面温升与速度变化之间的关系曲线如图2.6所示,其中载荷Fz=25.235kN,压力P0=770kPa,环境温度T0=15℃。
由图2.6可以看出,随着轮胎旋转速度的增加,轮胎稳态温升与速度之间呈线性关系增长,这个关系一直保持到临界速度,速度越高,温升越高。由于随着速度的增加,轮胎变形频率加大,弹性迟滞损失量增大,单位时间内生热量增加,因此轮胎温升变大。另外,由图中还可以看出,不同载荷下,温升与速度间的变化关系相同,且温升随载荷增加而增加。

图2.6 稳态时不同载荷下轮胎胎肩表面温升与速度的关系[24]
文献[24]利用实验数据进行线性回归,得到稳态时轮胎胎肩表面的温升ΔT与速度v之间的回归方程为:

根据式(2.8)的关系,不但可以确定车速是否合适,而且可以通过调整车速来进行温度的调节。当轮胎温度达到85℃时,车速不要超过240km/h;当轮胎温度达到90℃时,车速不要超过160km/h;当轮胎温度达到95℃时,最大车速必须低于80km/h;当轮胎温度达到100℃时,必须降低车速或立即停车。
稳态时,实验测试得到轮胎胎肩表面的温升与载荷的关系曲线如图2.7所示,其中载荷Fz=25.235kN,压力P0=770kPa,环境温度T0=15℃。
由图2.7可以看出,稳态时,轮胎胎肩表面的温升与载荷之间呈线性关系增长,载荷越大,轮胎表面的温升越大。由于随着载荷的增加,轮胎下沉量变大,轮胎所受的应力和应变量增大,因此,轮胎生热量增加,轮胎温升变大。在相同速度下,轮胎载荷由75%Fz增加至Fz,轮胎胎肩表面温度可上升5~8℃,轮胎内部最高温度则可上升20~30℃,可见,汽车超载运行时轮胎温升很大,极易发生热损坏。另外,从图中还可以看出,不同速度下的温升与载荷间的变化关系相同,并且温升随速度的增加而增加。比较图2.6和图2.7可以看出,在速度与载荷都增加25%而其他因素不变的情况下,由载荷变化引起的温升要比由速度变化引起的温升大,因此,载荷对温升的影响比速度对温升的影响大。

图2.7 稳态时不同速度下轮胎胎肩表面温升与载荷的关系[24]
文献[24]利用实验数据进行线性回归,得到稳态时轮胎胎肩表面的温升ΔT与载荷Fz之间的回归方程为:

稳态时,实验测试得到轮胎胎肩表面温升与轮胎压力的关系曲线如图2.8所示,其中载荷Fz=25.235kN,压力P0=770kPa,环境温度T0=15℃,速度v=90km/h。由图可以看出,稳态时,轮胎胎肩表面温升与轮胎压力之间呈反比例线性关系,轮胎压力越高,温升越小。由于随着轮胎压力的增加,轮胎刚度增大,轮胎变形量减小,轮胎生热量降低,因此轮胎温升变小,反之,轮胎压力越低,轮胎温升越大。

图2.8 稳态时轮胎胎肩表面温升与轮胎压力的关系[24]
根据图2.8的数据关系,文献[24]建立稳态时轮胎胎肩表面温升ΔT与轮胎压力P之间的回归方程为:

稳态时,实验测试得到轮胎胎肩表面温升与环境温度之间的关系曲线如图2.9所示,其中载荷Fz=25.235kN,压力P0=770kPa,速度v=90km/h。由图可以看出,稳态时,轮胎胎肩表面温升与环境温度之间呈线性关系增加,环境温度越高,轮胎胎肩表面的温升越大。由于随着环境温度的升高,轮胎表面散热困难,积聚在轮胎内部的热量增多,因此轮胎温升变高。
根据图2.9的数据关系,文献[24]建立稳态时轮胎胎肩表面温升ΔT与环境温度T0之间的回归方程为:

图2.9 稳态时轮胎胎肩表面温升与环境温度的关系[24]

轮胎在实际滚动过程中,外在因素中的速度、载荷、压力及环境温度常常发生变化,并且往往是多个因素同时发生变化,因此,建立轮胎表面稳态温度变化与各种外在因素之间的函数关系式具有重要的实际意义。文献[24]利用图2.5~图2.9的数据,通过多元回归技术,经过编程计算建立了9.00-2014 PR轮胎胎肩表面稳态温度与外在因素之间的回归方程为:

由式(2.12)可以看出,各因素对轮胎温升影响的次序依次为:载荷>环境温度>速度 >压力,可见载荷对轮胎表面温升的影响最大,这与文献[24]~[26]中实验研究所得到的结论一致。
文献[24]通过进一步的研究发现,在各种工况下,轮胎其他部位的温升与轮胎的速度、载荷、压力和环境温度之间的关系与式(2.12)的结果类似,只是各因素前的系数及常数项不同,各因素对轮胎表面温度的影响次序与式(2.12)所得结论相同,因此,轮胎表面的温升与轮胎速度、载荷、压力和环境温度之间为线性关系,并且轮胎表面温升随速度、载荷和环境温度的增加而增加,随轮胎充气压力的增加而降低。
根据前面的分析可以看出,轮胎的温度变化受到轮胎速度、载荷、压力和环境温度等外在因素的影响,因此,当轮胎的温度变化异常时,需要进行外在因素的综合判断,分析是否是外在因素引起的温度变化,是否可以通过外在因素的调节进行温度的调整,从而实现轮胎温度异常故障的智能诊断和处理,提高轮胎的安全性和经济性。