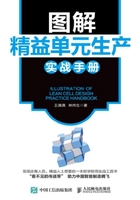
1.2 设备功能布局
设备功能(工艺导向)布局是把大致相同的设备或工艺集中摆放在同一个区域,对产品进行类似加工的一种布局方式。设备功能布局如图1-2所示。

图1-2 设备功能布局
例如,模具加工工厂把车床、铣床、钻床、线切割、加工中心放置在不同的区域,模具根据工艺路线的要求搬运到不同的区域进行加工。模具、冲压、钣金、注塑、机加工都会使用这种布局方式。在这种布局中,人们经常会出现一种惯性思维,看到冲压工厂就会采用设备功能布局,人们在潜意识里认为冲压本就应该通过设备功能布局来进行车间规划设计,而没有进一步思考为什么需要集中放置设备。设备功能布局在我们的工厂适用吗?能够给企业带来什么好处或坏处?其他企业采用设备功能布局的理由是什么?
设备功能布局的优势有以下4项。
1.有利于设备管理和人员管理
将相同的设备和作业人员放置在一起,减少变化,自然就能减少管理上的难度,管理者仅需要管理相同类型的设备和具有相同操作技能的员工即可。
2.有利于员工提高技能
单一技能或者少数技能重复使用,很容易锻炼作业人员的操作技能,容易培养出技术上的尖兵,但是这些尖兵在技术的广度应用上可能有所缺失。
3.设备故障影响最小
在相同区域内会有很多台同样的设备,如果一台设备出现了故障并不会影响产出,可以直接转到另一台设备进行加工,维修人员也相对更容易进行维修。同样的设备出现多次故障,而这些设备的原理和结构都是相似的,备件也更好管理。
4.调配设备产能负荷
设备集中摆放在一起很容易看出设备的负荷程度,也容易将满负荷设备的工作计划调配到其他设备进行生产。汇总加工工单可以提高设备的使用率,不会出现因为上游未加工完成而造成部分生产线环节等待的现象。
1.2.1 设备功能布局方式缺点1:搬运浪费
设备集中摆放,上下工序产品流转很不方便,搬运的具体工作需要搬运人员把产品从一个车间搬运到另一个车间,搬运的路线很长。如果车间在不同的楼层、不同的区域,距离会更远,除了搬运距离变长之外,搬运次数也会变多。为了节省搬运人员的时间,一般是要堆积了大量的产品之后才开始搬运,形成一天搬运一次或者两天搬运一次的习惯。此外,还要增加不少搬运人员和设施。设备类型的布局就是一种离散型的布置方式,增加了很多孤岛作业的情况,上下游的信息很难进行沟通和协调,从而造成了搬运的无序化,增加了异常搬运的频次。设备功能搬运如图1-3所示。

图1-3 设备功能搬运
为什么需要搬运?因为设备功能布局不合理,或者上下两个工序不连续、中间有隔断。有隔断就会出现搬运需求,将需要搬运的上下两个工序连接在一起,形成连续流的生产方式,这样就不会产生隔断,或者大幅减少需要搬运的概率。然而,按设备功能布局往往会将上下工序断开,从而产生大量需要搬运的工作。单独考虑搬运可能造成的浪费就是增加人员数量和工作时间,搬运过程产品工艺路线多样化、搬运次数多再加上生产没有进行先进先出(First Input First Output,FIFO)控制,就会形成所谓的乱流。FIFO是指先入库的材料先发出,按先入库的优先发出材料,发完该批再发后一批次。如果不按顺序则会造成先到货物长期堆积在仓库里,以及造成库存次序的混乱。有些人不太在意搬运产生的成本浪费,认为最多就是增加人员和设备,可是搬运产生的浪费不仅影响人力成本和设备成本,还会造成其他方面的浪费。
1.2.2 设备功能布局方式缺点2:产生乱流
在设备功能布局的生产条件下,经常会出现需要的物料没有办法准时送达的情况。各加工车间按照自己“最优化作业”排序,而不是按照组装车间产品计划排序,零件杂乱无章地向自己的车间输送过来,而要装配的产品却缺乏零件,暂时不装配的产品零件却在堆积。往往有人认为造成这种情况是由于没有制订好生产计划,或者生产计划没有被执行好。其实,出现这种问题的一部分原因是生产布局方式导致了产品乱流。产品乱流现象出现后,意味着所有的计划是失控的,原本安排这台设备生产,而该设备处于满负荷状态,因此需要移到另一台设备上生产,而另一台设备还在执行原先的运行计划。另外,当乱流现象出现后,管控产品的进度也失效了。设备功能乱流情况如图1-4所示。

图1-4 设备功能乱流情况
产生乱流的具体原因如下所述。
一是有几台相同的加工设备,根本没有办法确认是在哪台设备上加工,一般是看到哪台设备空闲就安排哪台设备,后续工序由其他几台设备加工,从而看到产品在设备之间无序、无规则地流动。产生乱流还因为不同的产品有不同的加工路径,一种产品可能不会产生乱流,但是当多种产品与不同的工艺路线混合在一起时就容易产生一团乱麻的现象。
二是每个加工区域都有大量的库存,库存并没有做到先进先出,这样就导致先到的产品没有及时生产,后到的产品反而先被安排生产。综合多种原因,再加上管理者没有特别干预协调,最后就出现了乱流现象。
当产品处于乱流状态时,生产进度把控和计划准时达成就会完全处于一种失效的状态,没有办法在规定的时间内生产出产品,就无法知道生产的产品处于哪个环节,还需要多长的时间才能够生产出产品。这时候就会出现更多的人工干预。例如,到现场查看产品进度;加班赶交货期;责令每个区域加快生产客户着急的订单;向客户解释为什么产品不能按时交货等。
1.2.3 设备功能布局方式缺点3:制造周期长
我在工厂里经常看到每个工段加工的时间很短,总共加起来几十分钟,可是从投入原材料到最后成品加工完成的制造周期,需要几天或者几个星期。那大量的时间都浪费在哪里呢?
批量加工过程需要时间来完成,完成加工的产品要停下来,等待所有产品加工完成。待产品加工完成后,需要等待搬运人员将产品搬运到下一个工序。到了下一个工序也不能马上生产,理由是生产工单里要求的生产时间没有到,产品无法提前生产。工序等待可能是因为物料短缺,也可能是因为生产线正在加工产品,需要等待正在加工的产品加工完毕,这些都会使产品的制造周期变长。设备功能布局下的等待浪费如图1-5所示。

图1-5 设备功能布局下的等待浪费
产品的制造周期长对企业生产有哪些影响?
1.减缓现金流周转次数
一元钱和十元钱代表的价值是不一样的,但是相同时间段内一元钱周转十次和十元钱周转一次所产生的价值是一样的。如果制造周期变长,现金流动速度将变缓,公司需要投入更多的现金,现金流一旦出现问题会导致企业经营受阻。
2.无法快速满足客户需要
客户临时变更交货日期。例如,从10天交货变为3天交货,在这种情况下,原来制造周期为3天的可以3天交货,但制造周期为10天的则无法满足客户3天交货的要求。如果无法快速满足客户的要求,则意味着客户将会减少相应的订单。
3.产生更多的库存
制造周期长的库存数量一定要比制造周期短的库存数量多,这是因为库存需要积压更长的天数、停留在工厂的时间更长,从而形成更多的库存。
4.降低竞争力
相同的价格、相同的品质,制造周期短的产品更受客户的喜欢。以购买汽车为例,现在市场上存在价格相近、品质相当的各种品牌汽车,在这种竞争环境下,短时间内能为客户提供新车就变成一种竞争优势。制造周期与库存有相同的功效,它们可以衡量一家企业的运营能力。库存量大意味着企业缺乏有效的管理方式或把很多问题用库存掩盖起来。库存量大、制造周期长的企业一定不是一家好的企业。
1.2.4 设备功能布局改善方向
设备功能布局的优点是作业人员管理容易(同一类的员工)、通用性强(所有的产品都在布局内生产)、故障不影响整体产出(一台设备损坏了还有其他备用设备可以生产)、作业人员培训周期短。尽管如此,一般不建议企业采用设备功能布局方式。有些企业因为自身行业的特殊性,认为在企业内部不存在(有办法针对缺点进行解决)设备功能布局的缺点,这样的企业就可以继续使用设备类型布局。设备功能布局可以采用连续流生产线或单元生产线方式,这不仅给企业带来了巨大的收益,还符合精益五大原则中关于创建连续流和实现连续生产的原则。
创建连续流在不同的行业存在不同的情况,最简单的改善方式是将原来离散的生产区域合并为一条生产线,生产线可以是流水线也可以是单元生产线。若原来离散的生产区域变为流水线以后,原来需要的搬运不需要了,作业人员可用“手递手”的传递方式代替。原来产品为乱流,现在产品可以有规律地从流水线的起始端流动到末端,直接变成成品,这样既容易安排计划也容易监控产品进度,还可以消除过程中的等待,使整体制造周期变短。单件流改善如图1-6所示。

图1-6 单件流改善
不同的布局方式具有不同的优点和缺点,设计布局时要结合产品的特点进行分析,适用的布局方式可以给生产制造环节带来不同的优势和劣势。布局的优势是我们选择它的理由,同时,我们要想办法克服布局的劣势。